Above Ground Tank Bottom Floor Inspection
Above Ground Tank Bottom Floor Inspection in India
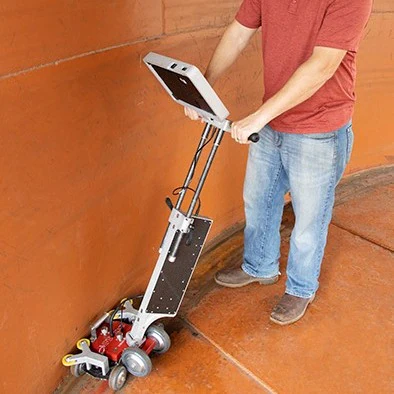
Above Ground Tank Bottom Floor Inspection using Magnetic Flux Leakage (MFL) is a crucial non-destructive testing (NDT) method to assess tank integrity. MFL detects corrosion, pitting, and defects without tank emptying. Inspection & Testing Engineers excels in providing MFL services for tank bottom floors. With vast experience and advanced MFL technology, they deliver precise and reliable inspections. Skilled technicians interpret MFL data accurately, ensuring comprehensive evaluations and timely maintenance. Their commitment to safety and customer satisfaction makes them the best choice for MFL services.
Inspecting the bottom floor of an above ground tank is a critical maintenance activity to ensure the integrity and safety of the tank. The tank bottom is susceptible to corrosion, pitting, cracking, and other forms of deterioration that can compromise the structural integrity of the tank and lead to leaks or spills. Here are the steps involved in conducting an above-ground tank bottom floor inspection:
1. Preparation and Safety:
- Ensure you have the necessary safety equipment, such as personal protective gear and gas detection equipment if the tank contains hazardous materials.
- Notify relevant personnel and follow proper safety protocols.
- Secure any necessary permits or permissions for the inspection.
2. Draining the Tank:
- If the tank is not already empty, it should be properly drained to a safe level. This might involve transferring the contents to another storage facility.
3. Cleaning the Tank Bottom:
- Remove any remaining liquid, sludge, or debris from the tank bottom. This might involve using vacuum trucks or other cleaning methods.
Ensure the tank bottom is dry and free from any residual contaminants.
4. Visual Inspection:
- Conduct a thorough visual inspection of the tank bottom using proper lighting and inspection tools.
- Look for signs of corrosion, pitting, cracking, weld defects, and other forms of damage. Pay close attention to areas prone to corrosion, such as the weld seams, and areas where moisture could accumulate.
5. Ultrasonic Testing (UT) or Magnetic Particle Testing (MT):
- Ultrasonic testing involves using sound waves to detect defects within the metal. It’s useful for detecting hidden cracks and thinning in the tank bottom.
- Magnetic particle testing uses magnetic fields and particles to identify surface and near-surface defects like cracks and discontinuities.
6. Repair and Maintenance:
- Address any identified issues promptly. This might involve repairing corroded areas, reinforcing weak sections, or applying new protective coatings.